The semiconductor industry may seem like a modern marvel, but its origins in the 1950s tell a fascinating story of innovation, challenge, and economic transformation.
Introduction
The 1950s mark a foundational decade in the history of the semiconductor industry. Building on the transistor’s invention in the late 1940s, this period laid the groundwork for manufacturing capabilities and rudimentary pricing frameworks that would define the path of the rapidly evolving sector. During these formative years, semiconductor products were expensive novelties with very specific niches. They were primarily used in military applications and high-end research projects rather than mass consumer markets. Demand was modest but growing, driven by the potential of these new devices to replace bulky vacuum tubes and usher in more compact, efficient electronic systems.
This first article in our decade-by-decade series explores how the fundamental cost drivers of the 1950s shaped pricing decisions, influenced broader market strategies, and paved the way for what would later become one of the world’s most transformative industries. By understanding the opportunities, constraints, and economic conditions of this period, we see how strategic decisions around pricing models formed the bedrock of semiconductor commerce.
The dawn of semiconductor manufacturing
Semiconductors were born out of intense research efforts to find alternatives to vacuum tubes in switching and amplification circuits. The invention of the transistor at Bell Labs in 1947 provided an impetus for developing early manufacturing processes in the early 1950s. While the theoretical concepts for semiconductors were well-understood within research circles, large-scale fabrication was a major challenge. Silicon’s potential was known, but germanium-based transistors initially dominated because germanium was easier to work with at lower temperatures.
Cost drivers in early production
Hand assembly: Early transistor production was extremely labor-intensive, leading to high unit costs. Much of the transistor assembly (mounting active junctions, attaching leads) and packaging the final device was done by skilled technicians using manual tools and microscopes. This constrained volume and inflated prices.
Low yields: Process inconsistencies (impure materials, doping challenges, mechanical handling) meant a large fraction of transistors failed testing, so the cost of each successful device had to absorb the expense of the rejects.
Small batches: Because demand was relatively low and yields were unpredictable, manufacturers produced semiconductors in small batches. Cost per device was often dictated by how many survived1 the fabrication process, which made pricing somewhat volatile.
Equipment and materials: Specialized equipment—much of it adapted from other fields such as glass-blowing and vacuum sealing—was expensive and scarce. Meanwhile, semiconductor-grade materials faced similar supply limitations, further driving up costs.
Research & development (R&D) overhead: in the 1950s, manufacturers were essentially learning on the job, refining processes with every batch. These R&D costs were often rolled into overhead, further raising per-transistor cost.
Cost element | Typical share of cost23 | Cost items |
---|---|---|
Materials | 20–30% | Included germanium (or early silicon) wafer/slug, alloy dots or point contacts, lead frames, and the metal or plastic package. |
Direct Labor | 30–50% | Reflects substantial manual labor: each transistor could take 15–30 minutes for delicate assembly and rework. |
Overhead & Indirect Costs | 20–40% | Low yields (often <10–20%) meant many devices were discarded during testing, raising the effective cost of each functioning transistor. Overhead also included the expense of specialized equipment, plus ongoing process R&D |
Table 1: For a typical mid-1950s transistor retailing at around $10 (nominal 1950s dollars), direct manufacturing costs (materials + direct labor + overhead) might run $6–$8, leaving a margin to cover distribution, marketing, and profit. Actual proportions varied by company and year.
Major industry events of the 1950s and their impact on pricing
Government-funded research
Driven by Cold War imperatives, the U.S. government poured millions4 into semiconductor R&D. The U.S. Department of Defense (DoD) provided funding for research and development, prioritizing performance and reliability over cost. Bell Labs and other institutions rapidly advanced transistor technology, enabling better yields and gradually bringing down manufacturing costs. With military applications at the forefront, producers had incentives to streamline processes, but defense spending largely shielded them from severe price pressure. Essentially, government funding allowed manufacturers to recoup large portions of their R&D investments, mitigating the need for aggressive cost-based pricing. To illustrate just how important the U.S. government was during these early days, in the 50s ~80-90% of semiconductor capacity was absorbed by the U.S. DoD – today, as consumer applications have taken over that figure is ~4%.
Entry of early innovators
Companies such as Texas Instruments and Fairchild Semiconductor entered the market in the late 1950s. Their approach to production and emphasis on research into silicon-based transistors helped reduce dependency on germanium, potentially lowering material costs once silicon processing was refined. This gradual shift introduced a measure of competition, modestly influencing pricing strategies by the decade’s end.
Transition from Germanium to Silicon
Though germanium was the initial workhorse, it had significant limitations, particularly regarding high-temperature performance. Silicon offered a wider operating temperature range and lower leakage current, which translated to more reliable devices. However, the switch to silicon required new equipment and manufacturing know-how—an upfront investment that temporarily sustained higher product prices. Despite these costs, silicon transistors eventually dominated, setting the stage for more cost-effective manufacturing in subsequent decades.Timeline of key pricing milestones in the 1950s
Manufacturing Costs and their influence on pricing
By the late 1950s, manufacturers were fully aware that improving yields could drive more aggressive pricing. Each step in the process—material purification, wafer slicing, device fabrication, and packaging—had its own inefficiencies. While the labor-centric model of production limited the speed at which costs could drop, incremental process refinements made a difference over time:
Material purity
With each improvement in crystal growth and doping techniques, the reliability of individual transistors increased, raising the effective yield. Cost-per-working-device therefore inched downward. This was instrumental in allowing for slightly lower end-user prices.
Packaging innovations
Packaging emerged as a crucial factor. Initially, transistors were encased in glass or metal cans. Better design and automation in packaging reduced defect rates. This not only cut production costs but also made transistors more robust, further fueling market demand.
Scale and learning curves
The concept of an experience curve—where costs fall as manufacturing volumes rise—was practically observable, though not formally studied in detail until later. Each batch run taught engineers how to refine temperatures, doping levels, and other parameters, gradually boosting yields.
Early pricing models
Three main pricing models emerged during the 1950s:
Premium pricing for novelty: The first transistors were priced high because they offered capabilities that vacuum tubes could not match. This premium was justified by lower power consumption, reliability, and form factor advantages. Defense and specialized research clients, who needed cutting-edge technology at almost any cost, were prepared to pay for it.
Bundled contract deals: For government and major commercial orders, semiconductor manufacturers often offered batch pricing or tiered discounts. This approach balanced manufacturers’ need for stable revenue streams against the procurement agencies’ push for cost containment.
Cost-plus in government contracts: Certain supply agreements with defense agencies were structured on a cost-plus basis, meaning the price was determined by actual manufacturing costs plus a fixed margin. While this model ensured profitability, it limited manufacturers’ incentives to drive down costs quickly—at least for the government portion of their business.
In hindsight, these early pricing structures directly reflected the small-scale, specialized nature of the nascent semiconductor sector. Without the broader commercial push that would come later, prices remained elevated, albeit slowly trending downward as volumes increased.
Approximate Cost Trend of a Single Transistor (1950–1959)
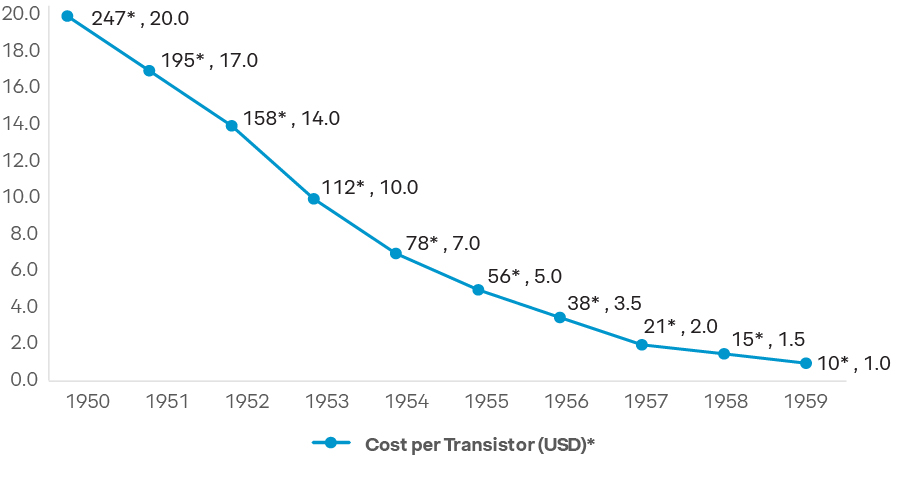
Figure 1: Approximate cost per single transistor 1950-1959; Approximate historical overview of cost per single (discrete) transistor from 1950 through 1959, based on data compiled from multiple historical and peer-reviewed sources. Because transistor manufacturing was still in its infancy through most of the 1950s, data on exact prices vary widely; the figures below should be interpreted as representative estimates. *2023 Inflation adjusted cost derived from BLS data (1950-2023).
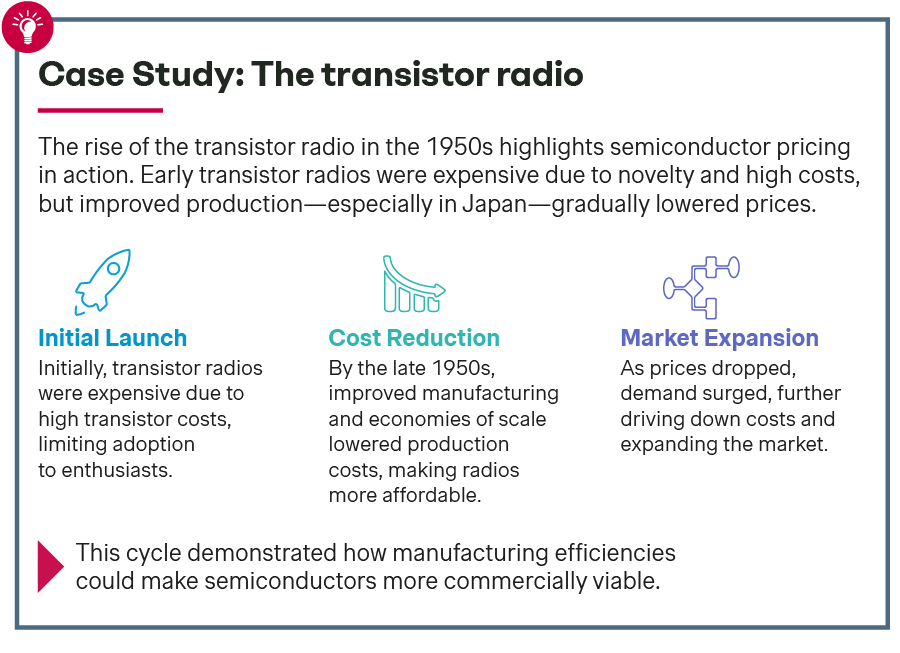
Conclusion: The 1950s – the foundations of an Industry
The 1950s laid the essential framework for semiconductor pricing strategies that would evolve in later decades. Dominated by small-scale manufacturing, labor-intensive processes, and dependence on government funding, the industry was still in its infancy. The high cost of semiconductors reflected both their scarcity and their strategic importance to defense and specialized electronic systems.
Yet, even in this early period, we observe the seeds of future developments: the shift to silicon as the favored material, the reliance on yield improvements to reduce costs, and the gradual emergence of private sector demand through products like transistor radios. In the context of pricing, the critical driver was the relationship between yield enhancement and manufacturing scale. The tiny leaps in process refinement paved the way for slightly lower unit costs and expanded the pool of end-user applications.
Key lessons
The decade underscores that price reduction in semiconductors has always hinged on both technological innovation and manufacturing refinement. Even in the 1950s, we see that modest scale increases and improved yields can unlock new markets by making the product more affordable. While the industry was still learning how to mass-produce at acceptable defect levels, the foundational strategies of cost management—materials research, process automation, and yield optimization—were already set in motion.
In future decades, these early lessons would be magnified many times over. As we progress into the 1960s in our next article, the introduction of the integrated circuit and further improvements in scale will radically shift the pricing conversation, paving the way for an industry that would transform modern technology and global markets.